Revolutionizing Filtration With Advanced Drum Filters
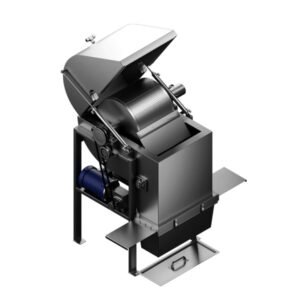
Drum filters have become an essential innovation for continuous extraction applications in industries such as botanicals, gums, and contaminated materials. This versatile system provides a seamless process to build, extract, and refresh filter cakes while maintaining efficient throughput and high extraction yields.
What is a Drum Filter?
A drum filter is a filtration device widely used in industrial applications for particle filtration or solid-liquid separation. Its main component is a rotating cylindrical drum partially submerged in a liquid mixture or slurry. The drum’s surface is covered with a porous filter medium that allows liquid to pass through while stopping solid particles.
Drum filters operate continuously, making them highly sought after for their ability to handle large volumes of material. Depending on the specific design, filtration can be done using vacuum pressure, positive pressure, or gravity to draw the liquid through the filter medium.
Types of Drum Filters and Their Applications
There are many types of drum filters, including Rotary Vacuum Drum Filters, Rotary Pressure Drum Filters, Horizontal Drum Filters, and Micro Drum Filters. Choosing the right drum filter depends on the specific application, flow rates, particle retention needs, and maintenance considerations. Each type offers unique features to tackle many particle filtration challenges effectively.
Rotary Vacuum Drum Filters
Rotary vacuum drum filters are distinguished for their low-energy requirements and their ability to separate solids from liquids with a vacuum. As the drum rotates through slurries, a vacuum draws liquid through a filter, leaving behind a cake of solids. This system is proficient at continuous operation with minimal operator attention, suitable for dewatering a wide range of waste streams.
The food processing industry, for instance, utilizes rotary vacuum drum filters for the clarifying of fruit juices and edible oils. In the field of mining and minerals, these filters contribute to dewatering fine coal and tailings. The pharmaceutical industry also integrates rotary vacuum drum filters to filter out precipitates from bulk drugs, ensuring product purity and safety.
Rotary Pressure Drum Filters
Contrasting their vacuum counterparts, Rotary Pressure Drum Filters operate under pressure to increase the particle filtration rate. These drum filters excel in scenarios where faster dewatering of thin sludges is needed. Due to pressurization, these systems can release drier solids and more purified effluents. Moreover, the processing of aluminum, petrochemicals, and dyes are areas that benefit from the high-throughput processing of pressure drum filters.
Micro Drum Filters
Micro Drum Filters are engineered to provide ultra-fine particle filtration. They are commonly seen in applications such as aquaculture, where water clarity is critical. With their high-precision particle filtration capabilities, these filters effectively remove fine particulate matter, enhancing water quality and reducing the load on subsequent treatment stages.
How a Drum Filter Works
The most popular and most used drum filter across all industries are rotary vacuum drum filters, from wastewater treatment to mining to food and beverage and to chemical processing.
Rotary vacuum drum filters focus on the filtration of particles from a fluid. This technology utilizes a rotating cylindrical drum, relying on both gravity and vacuum suction for particle filtration. As the drum spins in the fluid, a vacuum through the filter’s internals sucks the liquid through a filter media on the drum’s surface, leaving a cake of solids.
The process starts with submerging the drum in a trough of the slurry, with a portion of the drum exposed to the atmosphere. The drum’s surface is covered with a filter cloth or other media and rotates slowly. As the vacuum applies suction, it draws the liquid through, depositing solids on the media, thus creating a layer of solid material known as the filter cake.
As the drum rotates, the filter cake is lifted from the slurry and dries partially due to the vacuum. Advancing further, the drum encounters a knife or a scraper, which removes the filter cake from the media’s surface. Then, a wash spray can clean the filter media before it dips back into the slurry, allowing the process to continue.
Rotary Vacuum Drum Filter Benefits
Since rotary vacuum drum filters are the most popular filters used across industries, there must be a reason. So, let’s look at their benefits.
Efficiency Through Continuous Operation
Rotary vacuum drum filters operate continuously, making them indispensable for industries that require constant, uninterrupted particle filtration. Unlike batch systems that require frequent halts, rotary vacuum drum filters provide seamless processing, reducing downtime and increasing overall efficiency. They deliver clear filtrates and consistent filter cakes, even when handling challenging slurries.
Versatility
The versatility of rotary vacuum drum filters makes them suitable for various industries and materials. They can adapt slurries with different particle sizes and concentrations, making them adjustable to changing process requirements. This flexibility allows industries to use a single filtration solution for diverse needs.
Cost-effective
Rotary vacuum drum filters are also highly cost-effective, thanks to their simple design and durable components. They require minimal energy input compared to other particle filtration methods, and their ability to run continuously reduces labor costs and operational expenses. Over time, this makes them a budget-friendly choice for many businesses.
Easy Maintenance
Finally, easy maintenance further improves the allure of rotary vacuum drum filters. The filter media and mechanical components are accessible and easy to replace, ensuring minimal downtime during repairs or cleaning. Easy maintenance ensures reliable, long-term performance with less effort and expense.
DRUMDROYD: The Revolutionary Rotary Vacuum Drum Filter
Our drum filter apparatus, the DRUMDROYD, is engineered for high-efficiency, continuous filtration applications and is ideal for handling challenging materials such as gums, waxes, or substances prone to filter fouling. From variable RPM control to an adjustable skiving knife, our DRUMDROYD is a cut above the rest. Contact us today to dive into your filtration journey!